Aircraft Fuselage: Design, Structure, Types & Materials
The aircraft fuselage is the central body of an airplane, housing passengers, crew, and cargo. Understanding its design, structure, and materials is crucial for aviation enthusiasts, prospective buyers, and maintenance professionals alike. This article breaks down the complexities of aircraft fuselages, covering various types, construction methods, and the use of materials like aluminum and composites. It also highlights common issues and maintenance considerations. Gojets offers expert guidance in aircraft sales, purchases, and maintenance, ensuring your aviation needs are met with precision and care. Contact us to learn more.
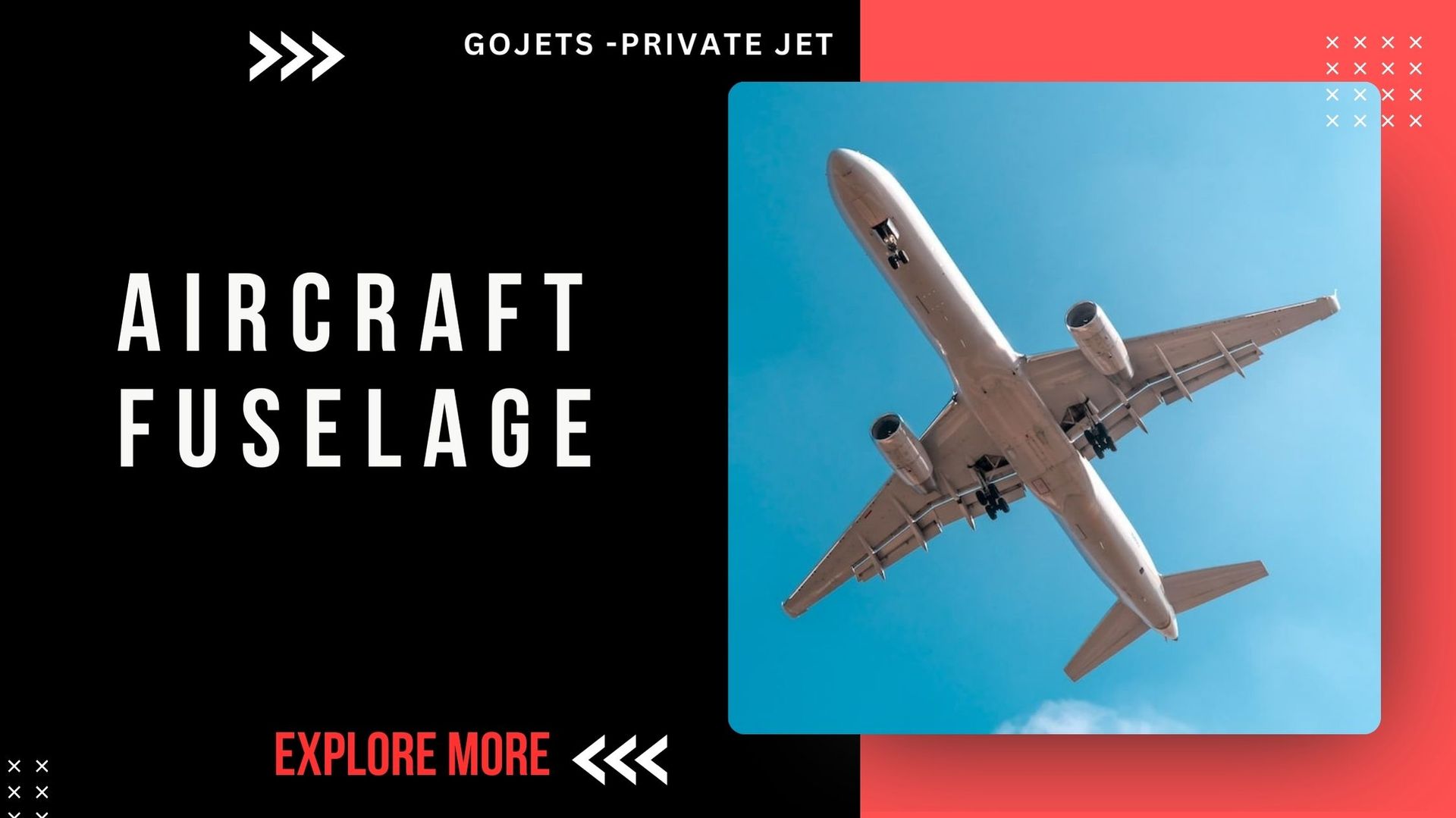
Understanding the Aircraft Fuselage
What is an Aircraft Fuselage?
The aircraft fuselage is the central body of an airplane, often referred to as the airplane body or airplane frame. It serves as the primary structure to which other essential aircraft components, such as the wings, tail, and landing gear, are attached. The fuselage houses the passenger compartment, cargo hold, and cockpit, accommodating passengers, crew, and cargo. It's designed to be both strong and lightweight.
Essentially, the fuselage acts as the core of the aircraft, providing a secure and controlled environment. Its shape and construction are critical for the overall performance and safety of the aircraft. Different types of aircraft have fuselages designed to meet specific needs, whether it's for carrying a large number of passengers, transporting heavy cargo, or achieving high speeds. This central structure ensures everything stays together during flight.
The design of the fuselage varies depending on the aircraft's purpose. For instance, commercial airliners have a tubular shape to maximize space and efficiency, while fighter jets might have a more streamlined design to enhance speed and agility. Regardless of the specific design, the fuselage remains a fundamental part of any aircraft, ensuring its structural integrity and operational capability. Proper maintenance of the fuselage is crucial.
The Purpose and Importance of the Fuselage
The fuselage plays a vital role in ensuring the safety and efficiency of an aircraft. Its aerodynamic properties are crucial for stable flight, influencing factors like lift and drag. A well-designed fuselage contributes to the aircraft's overall aerodynamic performance, reducing fuel consumption and improving stability. It also maintains the structural integrity of the aircraft.
Moreover, the fuselage is responsible for distributing forces evenly throughout the aircraft during flight, such as lift, weight, thrust, and drag. This even distribution prevents excessive stress on any single component, enhancing the aircraft's longevity and safety. The fuselage also protects occupants and internal systems from external elements like wind, rain, and extreme temperatures. It provides a secure environment.
Another critical function of the fuselage, particularly in commercial aircraft, is to provide a pressurized environment. The pressurized fuselage maintains a safe and comfortable cabin pressure at high altitudes, where the outside air pressure is too low for humans to breathe. This pressurization is essential for passenger and crew well-being during high-altitude flights, preventing altitude sickness and other related issues.
Etymology of "Fuselage"
The term "fuselage" has an interesting linguistic history. It is derived from the French word "fuselé," which means "spindle-shaped." This etymology reflects the typically streamlined, elongated shape of many aircraft fuselages, resembling a spindle. This connection highlights how language can provide insights into design and function. The term was adopted into English.
The evolution of aircraft design has seen various fuselage shapes, but the essence of a streamlined body has remained consistent. This linguistic root underscores the importance of aerodynamic efficiency in aircraft design, a principle that has guided engineers and designers for over a century. Understanding this origin can give us a deeper appreciation for the thought and history behind aircraft design. The word remains relevant today.
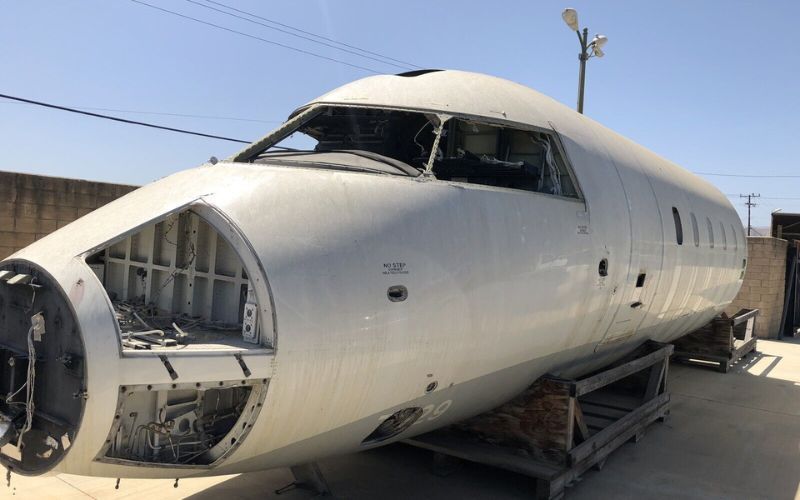
Exploring Different Types of Aircraft Fuselage Structures
Truss Structure Fuselage
Truss structure fuselages are constructed using a framework of beams, typically made from wood, steel, or aluminum tubing. This design creates a rigid structure where the strength comes from a series of interconnected triangles. This type of fuselage is commonly found in lightweight aircraft, such as small private planes and older models. The framework is often covered with fabric or a thin metal skin.
The use of materials like steel tube and aluminum tubing allows for a strong yet lightweight structure. This is particularly advantageous for smaller aircraft where weight is a critical factor. Examples of aircraft using truss structures include the Piper Cub and early biplanes. These designs are relatively simple to construct and repair, making them suitable for certain applications. The structure provides good strength.
While truss structures are effective for lightweight aircraft, they are less common in modern, larger aircraft. This is due to their lower strength-to-weight ratio compared to other designs. However, they remain relevant in specific niches of aviation where their simplicity and ease of maintenance are valued. Truss structures are still used today in some ultralight and experimental aircraft. They offer a practical solution.
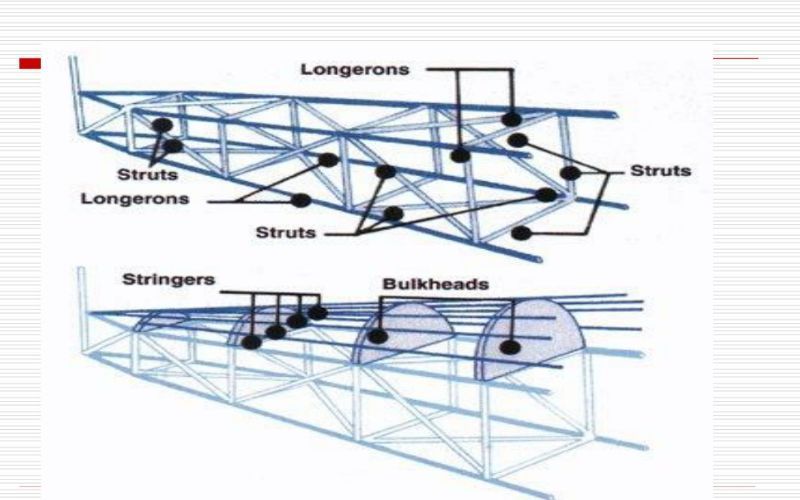
Geodesic Construction Fuselage
Geodesic construction is a unique method characterized by the use of spirally wound flat strip stringers, forming a basket-weave pattern. This design provides exceptional strength and redundancy, as the load is distributed across the entire structure. Materials used in geodesic fuselages include wood, aluminum alloy, and molded plywood. The aircraft skin is typically applied over this framework, creating a robust and resilient structure.
One of the key advantages of geodesic construction is its resistance to localized damage. Even if a portion of the structure is damaged, the surrounding framework can continue to support the aircraft. This inherent redundancy enhances safety and was notably used in the Vickers Wellington bomber during World War II. The design allowed the aircraft to withstand significant damage and still return safely.
While geodesic construction is not as common in modern aircraft, its principles have influenced the development of composite materials and structures. The concept of distributing loads across a network of interconnected elements is still relevant in contemporary aircraft design. This method showcases an innovative approach to achieving structural integrity and durability.
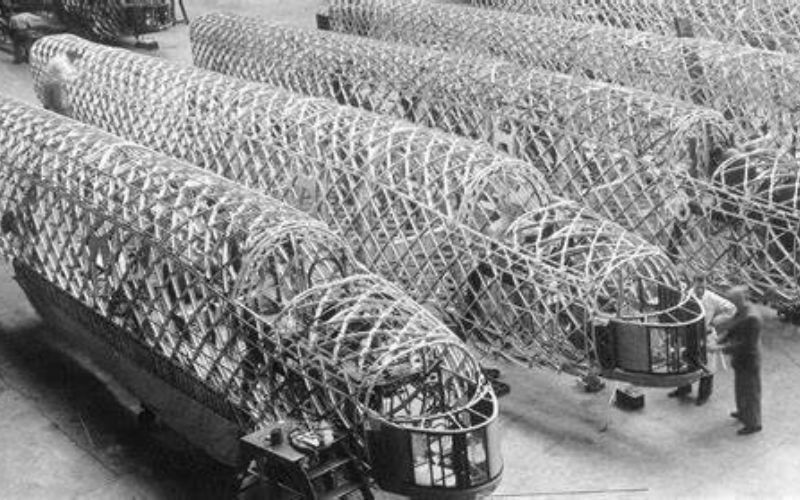
Monocoque Fuselage
Monocoque fuselages feature a design where the outer skin, or stressed skin, serves as the primary structural element. This means that the skin itself bears most of the structural loads, eliminating the need for a heavy internal framework. Early monocoque designs used materials like molded plywood or fiberglass, while modern aircraft like the Boeing 787 utilize advanced composite materials. This results in a very strong fuselage.
The monocoque structure offers a high strength-to-weight ratio, making it ideal for larger aircraft where weight savings are crucial. The Boeing 787, for example, features a composite fuselage that significantly reduces weight compared to traditional aluminum designs. Stiffening elements are often incorporated to support concentrated loads, such as around windows and doors. This type of structure is highly efficient.
While monocoque designs are strong, they can be more susceptible to damage from impacts or stress concentrations. A puncture or crack in the skin can compromise the integrity of the entire structure. Despite this, advancements in materials and manufacturing techniques have made monocoque fuselages increasingly popular in modern aircraft. They offer significant advantages in terms of performance.
Semi-Monocoque Fuselage
The semi-monocoque structure is the most common type used in modern aircraft, including models like the Airbus A350. This design combines a stressed skin with an internal substructure consisting of formers and stringers. Sheet aluminum is commonly used, with components attached through riveting or bonding. This hybrid approach provides both strength and flexibility in design, making it suitable.
This framework provides additional support and helps distribute loads evenly, while the stressed skin contributes to the overall strength. Semi-monocoque fuselages are well-suited for mass production, as they can be constructed using fixtures that ensure consistency and precision. The use of sheet aluminum and advanced bonding techniques also allows for efficient manufacturing processes. This design is highly adaptable.
The Airbus A350, for example, utilizes a semi-monocoque structure made primarily of aluminum alloys, resulting in a lightweight yet robust airframe. This design offers a balance of strength, weight, and ease of manufacturing, making it the preferred choice for many modern aircraft. The semi-monocoque structure represents a significant advancement in aircraft design, combining the best elements of earlier construction methods. This is why it's so prevalent.
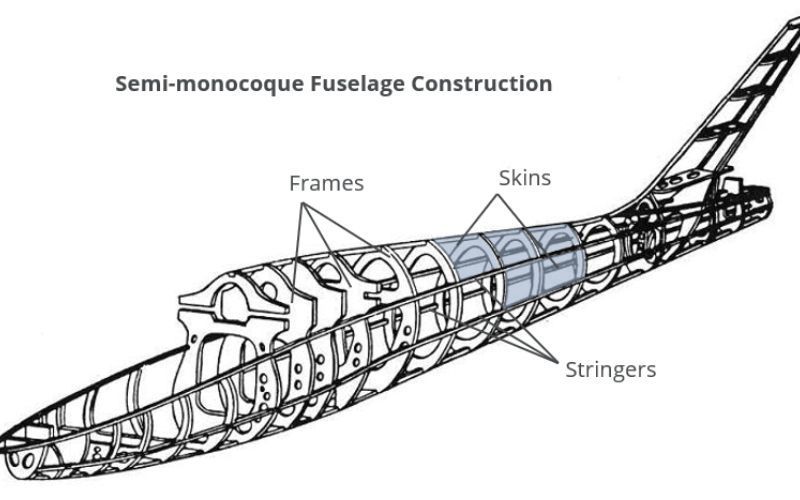
Aircraft Fuselage Materials: From Wood to Composites
Traditional Materials
The earliest aircraft fuselages were constructed using wood and fabric. Wood provided a lightweight yet relatively strong frame, while fabric stretched over the frame created a smooth, aerodynamic surface. However, these materials were susceptible to rot, weather damage, and lacked durability. As aviation advanced, the need for stronger, more resilient materials became evident, leading to the adoption of all-metal aircraft. All-metal aircraft were a big step.
Aluminum, particularly an alloy known as duralumin, quickly became the material of choice for aircraft fuselages. Duralumin, which combines aluminum with copper and other elements, offers an excellent balance of strength, and lightweight. It is also resistant to corrosion, a crucial factor for aircraft operating in various environments. Furthermore, aluminum is relatively affordable compared to other metals with similar properties, making it economically viable.
The use of aluminum revolutionized aircraft design, enabling the construction of larger, faster, and more durable aircraft. Aluminum's properties allowed for the development of monocoque and semi-monocoque fuselages, which rely on the strength of the outer skin. This shift to all-metal aircraft marked a significant milestone in aviation history, paving the way for modern aircraft design. Aluminum remains a primary material.
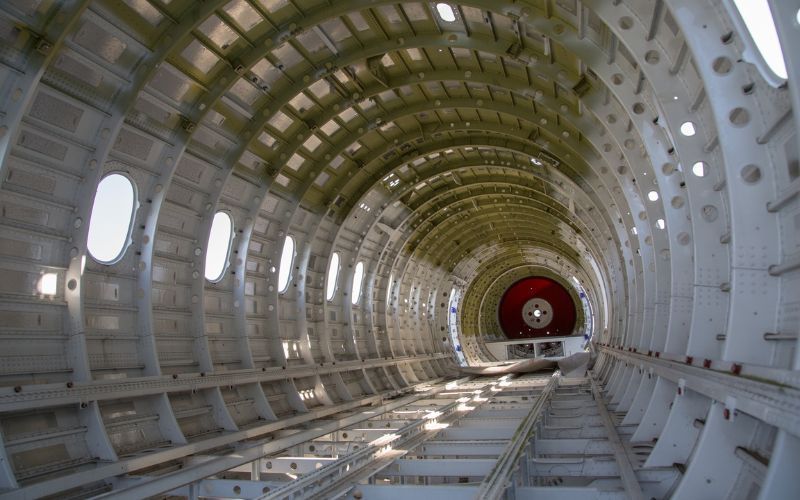
Modern Composite Materials
In recent decades, composite materials have increasingly been used in aircraft construction, including fuselages, wings, and control surfaces. Composites, such as carbon fiber and glass fiber, offer several advantages over traditional metals. One key benefit is their flexibility in design, allowing for complex aerodynamic shapes that are difficult to achieve with metal. Composites also provide higher strength.
Another significant advantage of composite materials is their superior strength-to-weight ratio. This means that components made from composites can be both stronger and lighter than those made from aluminum. This weight reduction translates to improved fuel efficiency and performance. Additionally, some composites have the ability to be reshaped or reformed after the initial molding process, providing greater flexibility in manufacturing and modification.
The use of composite materials has enabled the development of aircraft with enhanced performance characteristics. For instance, the Boeing 787 extensively uses composite materials, including a composite fuselage, resulting in a lighter, more fuel-efficient aircraft. While composites are generally more expensive than aluminum, their benefits often outweigh the higher initial costs, particularly for high-performance aircraft where weight savings are critical. They offer significant advantages.
Key Features of an Aircraft Fuselage
Windows and Windshields
Cockpit windshields and cabin windows are critical components of an aircraft fuselage, each with specific design requirements. Cockpit windshields are typically made from strengthened glass or high-strength plastics, designed to withstand impacts, such as bird strikes. They often incorporate multiple layers and heating elements to prevent fogging and ice buildup, ensuring clear visibility for the pilots. These are crucial for safety.
Cabin windows, on the other hand, are usually constructed from stretched acrylic glass. This material is lightweight, durable, and provides excellent optical clarity. Cabin windows typically consist of multiple panes: an outer pressure pane that bears the pressure load, a middle redundancy pane for safety, and an inner scratch pane for passenger comfort. This multi-pane design ensures that even if one pane is damaged, the cabin remains pressurized.
The design and construction of both windshields and cabin windows are crucial for maintaining the structural integrity of the fuselage and ensuring passenger and crew safety. They must withstand the stresses of flight, including pressure differentials, temperature variations, and potential impacts. Regular inspections and maintenance are essential to ensure their continued airworthiness. Proper care is very important.
Wing Integration and Blended Wing Bodies
Traditional aircraft designs feature a distinct fuselage and wings. However, some unconventional designs, such as "flying wing" aircraft and blended wing bodies, blur this distinction. In these designs, the fuselage itself is shaped to generate lift, contributing to the overall aerodynamic efficiency of the aircraft. This integration of wing and fuselage can lead to significant improvements in fuel efficiency and performance.
Blended wing bodies represent a more gradual transition between wing and fuselage, creating a smoother, more aerodynamic shape. This design reduces drag and increases lift, resulting in improved fuel efficiency. While still largely experimental, blended wing bodies have the potential to revolutionize aircraft design, offering significant advantages in terms of performance and environmental impact. They are the future.
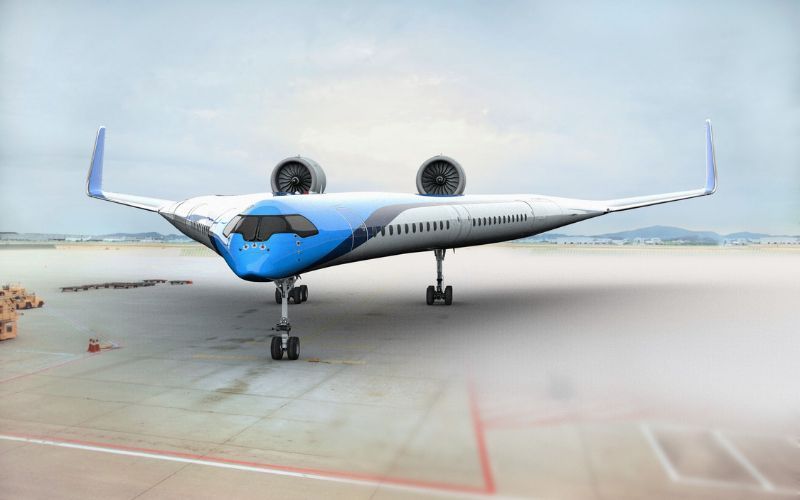
These innovative designs demonstrate the ongoing evolution of aircraft fuselage concepts. By rethinking the traditional separation of wing and body, engineers are exploring new ways to enhance aircraft performance and efficiency. While still in the early stages of development, these concepts hold promise for the future of aviation. They could change air travel.
Bulkheads and Pressure Control
Bulkheads are essential structural components within an aircraft fuselage, serving multiple critical functions. They are typically vertical walls or partitions that divide the fuselage into separate sections. One of their primary roles is to provide structural support and help distribute loads evenly throughout the fuselage. They are vital for strength.
In pressurized aircraft, specialized pressure bulkheads are used to seal the ends of the pressurized cabin. These bulkheads are designed to withstand the significant pressure differentials between the inside and outside of the aircraft at high altitudes. They are crucial for maintaining a safe and comfortable cabin environment for passengers and crew. Proper sealing is essential.
Pressure bulkheads play a vital role in maintaining the structural integrity of the pressurized fuselage. They must be carefully designed and constructed to withstand the stresses of flight and ensure the safety of everyone on board. Regular inspections and maintenance of bulkheads are essential to ensure their continued airworthiness. They are a key safety feature.
Classifications of Aircraft Fuselages
Wide-Body vs. Narrow-Body Aircraft

Aircraft fuselages are often classified as either wide-body or narrow-body, primarily based on their width and passenger capacity. Narrow-body aircraft, such as the Boeing 737 or Airbus A320, typically have a single aisle running down the center of the cabin, with seats arranged on either side. These aircraft usually accommodate fewer passengers and are commonly used for short to medium-haul flights. They are very popular.
Wide-body aircraft, in contrast, feature two aisles, allowing for a wider fuselage and greater passenger capacity. Examples include the Boeing 747, 777, and Airbus A380. These aircraft are typically used for long-haul international flights, offering more space and comfort for passengers. The wider fuselage also allows for more seating configurations and amenities, such as larger overhead bins and in-flight entertainment systems. These planes are larger.
The distinction between wide-body and narrow-body aircraft is significant in terms of passenger experience and operational capabilities. Wide-body aircraft generally offer more space and comfort, while narrow-body aircraft are often more fuel-efficient for shorter routes. The choice between these types depends on factors such as route length, passenger demand, and airline strategy. Each type has its advantages.
Lattice (Tubular) Fuselages
Lattice fuselages, also known as tubular fuselages, represent one of the oldest forms of aircraft construction. This type of fuselage is constructed using a network of steel tubes that are joined together to form a rigid framework. The framework is then typically covered with fabric or a thin metal skin to create the external shape of the aircraft. This is an older style.
Historically, lattice fuselages were common in early aircraft designs due to their simplicity and ease of construction. The use of steel tubes provided a relatively strong and lightweight structure. However, as aviation technology advanced, lattice fuselages were largely replaced by monocoque and semi-monocoque designs, which offer greater strength and aerodynamic efficiency. They are less common now.
While lattice fuselages are rarely used in modern commercial aircraft, they can still be found in some smaller, lightweight aircraft and historical replicas. They represent an important step in the evolution of aircraft design, showcasing the ingenuity of early aviation pioneers. Their simplicity is noteworthy.
FAQs about Aircraft Fuselages
How much does it cost to repair an aircraft fuselage?
Repair costs for an aircraft fuselage can vary widely, ranging from a few thousand dollars to millions, depending on several factors. Minor repairs, such as patching a small dent or replacing a damaged window, might be relatively inexpensive. However, major structural damage, such as that caused by a hard landing or severe corrosion, can be extremely costly to repair.
The specific type of aircraft, the materials involved, and the labor costs in a particular region also influence the overall expense. Repairs involving composite materials, for example, often require specialized equipment and expertise, which can add to the cost. Additionally, the extent of disassembly and reassembly required for the repair can significantly impact labor hours.
It's important to note that proper maintenance and timely repairs can help prevent minor issues from escalating into major, costly problems. Regular inspections and adherence to manufacturer-recommended maintenance schedules are crucial for minimizing long-term repair costs.
What are the most common materials used in aircraft fuselages today?
The two most common materials used in modern aircraft fuselages are aluminum alloys and composite materials. Aluminum alloys, particularly those containing elements like copper, zinc, and magnesium, have long been favored for their combination of strength, light weight, and corrosion resistance. They are also relatively affordable and easy to work with, making them a popular choice.
Composite materials, such as carbon fiber and glass fiber reinforced polymers, have gained increasing prominence in recent years. These materials offer even higher strength-to-weight ratios than aluminum, allowing for lighter and more fuel-efficient aircraft. They also provide greater flexibility in design and can be molded into complex aerodynamic shapes.
While both aluminum alloys and composites have their advantages, the choice of material often depends on the specific requirements of the aircraft. High-performance aircraft, where weight savings are paramount, often utilize a higher percentage of composites. In contrast, many commercial airliners still rely heavily on aluminum alloys due to their proven track record and cost-effectiveness.
How are aircraft fuselages inspected for damage?
Aircraft fuselages are inspected for damage using a variety of methods, ranging from simple visual inspections to advanced non-destructive testing (NDT) techniques. Visual inspections are the first line of defense, with technicians carefully examining the exterior and interior of the fuselage for any obvious signs of damage, such as dents, cracks, or corrosion. This is the first step.
For more in-depth inspections, various NDT methods are employed. These techniques allow inspectors to detect hidden flaws or damage that may not be visible to the naked eye. Common NDT methods include ultrasonic testing, which uses sound waves to detect internal cracks or voids; eddy current testing, which uses electromagnetic fields to identify surface and near-surface defects; and radiographic testing, which uses X-rays or gamma rays to create images of the internal structure.
Regular inspections are crucial for ensuring the continued airworthiness of an aircraft. The frequency and type of inspections required depend on factors such as the aircraft's age, usage, and operating environment. Adherence to manufacturer-recommended inspection schedules is essential for maintaining safety and preventing costly repairs down the line.
What is the lifespan of an aircraft fuselage?
The lifespan of an aircraft fuselage is influenced by numerous factors, including the quality of maintenance, the aircraft's usage patterns, and the materials used in its construction. An aircraft that is meticulously maintained and operated within its design limits can have a significantly longer lifespan than one that is neglected or subjected to excessive stress.
Flight cycles (takeoffs and landings) and flight hours are key metrics used to track fuselage lifespan. Each flight cycle subjects the fuselage to pressurization and depressurization stresses, which can contribute to material fatigue over time. Similarly, the total number of flight hours an aircraft accumulates is a crucial indicator of wear and tear.
Regular inspections and timely repairs are essential for extending the operational life of a fuselage. By addressing minor issues promptly, operators can prevent them from developing into more significant problems that could ultimately limit the fuselage's lifespan. Advancements in materials science and manufacturing techniques have also contributed to increased fuselage longevity in modern aircraft.
How does pressurization work inside an aircraft fuselage?
Pressurization is essential for maintaining a safe and comfortable environment for passengers and crew at high altitudes. The system works by using compressors, typically driven by the aircraft's engines, to draw in outside air and compress it. This compressed air is then cooled and circulated throughout the cabin.
A system of valves, known as outflow valves, regulates the flow of air out of the fuselage, maintaining a constant cabin pressure. This pressure is typically equivalent to the atmospheric pressure at a much lower altitude, usually around 6,000 to 8,000 feet. This ensures that occupants can breathe normally and avoid the effects of hypoxia, which can occur at high altitudes where the air pressure is too low.
The fuselage itself is designed to be airtight, with seals around doors, windows, and other openings to prevent air leakage. Pressure bulkheads at the front and rear of the cabin help to maintain the pressure differential between the inside and outside of the aircraft. The pressurization system is a critical safety feature, and its proper functioning is essential for high-altitude flight. It is vital for safety.
GoJets - Providing Expertise for Your Aircraft Fuselage Needs
Gojets offers a comprehensive range of services to meet all your aircraft needs, from sales and acquisition to maintenance and inspections. Our team of experts has in-depth knowledge of aircraft fuselages, including the various types, materials, and construction methods used in the industry. We can provide invaluable guidance in selecting the perfect aircraft to suit your specific requirements, whether you're considering a new or pre-owned aircraft. Gojets is here to help.
We specialize in both new and pre-owned aircraft sales, offering a wide selection of models to choose from. Additionally, Gojets provides fractional
ownership programs, allowing you to enjoy the benefits of aircraft ownership without the full financial commitment. Our specialized maintenance and inspection services ensure that your aircraft remains in optimal condition, maximizing its lifespan and ensuring your safety. We offer tailored solutions.
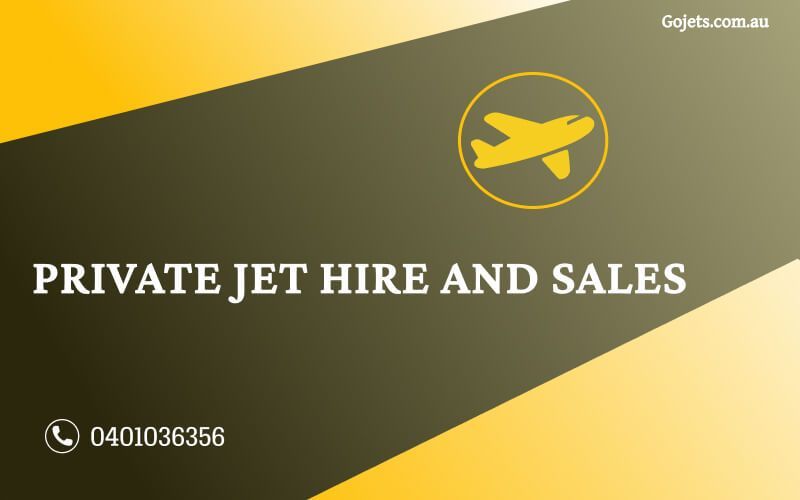
Read More:
- What is a Charter Plane? Private Jet Charter Explained
- Understanding Decision Height (DH) in Aviation: A Complete Guide
- Fastest Jets in the World: Top Speed Records & Future of Flight
The aircraft fuselage is a fundamental component of any aircraft, serving as the central body that houses passengers, crew, and cargo while connecting essential components like the wings and tail. Throughout this article, we've explored the different types of aircraft fuselages, from traditional truss and lattice structures to modern monocoque and semi-monocoque designs. We've also examined the evolution of fuselage materials, from early wood and fabric constructions to the advanced aluminum alloys and composite materials used today.
Understanding the intricacies of aircraft fuselages, including their construction methods, materials, and key features, is crucial for anyone involved in the aviation industry, whether as an enthusiast, a prospective buyer, or a maintenance professional. The fuselage plays a critical role in ensuring the safety, efficiency, and overall performance of an aircraft. Its design and construction have evolved significantly over the years, driven by advancements in technology and the ongoing pursuit of improved performance.
Whether you're looking to buy, sell, or maintain an aircraft, Gojets offers the expertise and services to meet your needs. Our team can guide you through the complexities of aircraft fuselages, helping you make informed decisions that align with your specific requirements. Contact Gojets today for expert advice and assistance with all your aircraft needs. Let us help you navigate the world of aviation